La lévitation acoustique consiste à suspendre de la matière dans un milieu, par opposition à la gravité, en utilisant la pression de rayonnement acoustique d’ondes sonores intenses. Cette manipulation sans le moindre contact physique présente un grand intérêt pour certaines applications industrielles et scientifiques. Des chercheurs de l’Université publique de Navarre ont développé un tout nouveau système basé sur cette technologie, capable d’assembler de petites structures en 3D.
Le système, baptisé LeviPrint, est véritablement révolutionnaire : la lévitation de petites particules et de gouttelettes avait déjà été réalisée auparavant, mais aucune équipe n’avait jusqu’à présent réussi à piéger des objets dans une position et une orientation bien précises. Combiné à un bras robotique et à un distributeur de liquide, ce système de lévitation peut servir à assembler des structures extrêmement sensibles et fragiles sans le moindre contact (ni humain ni matériel).
« Nous pouvons manipuler des pièces petites et fragiles, ainsi que des liquides ou des poudres, ce qui rend les processus plus polyvalents. Il y a moins de contamination croisée, car le manipulateur ne touche pas le matériau », a déclaré Iñigo Ezcurdia, doctorant à l’Université publique de Navarre (UPNA/NUP) et auteur principal de la recherche. Cette technique offre également des possibilités qui ne sont pas permises en impression 3D traditionnelle, telles que l’ajout d’éléments sur des pièces existantes ou à l’intérieur de conteneurs fermés.
Réorienter les pièces à volonté, sans les toucher
Contrairement aux techniques d’assemblage et de fabrication ordinaires, dans lesquelles les pièces sont en contact direct avec la machine, la lévitation acoustique permet ici de positionner et d’orienter les pièces sans les toucher pendant tout le processus. Le LeviPrint permet ainsi d’utiliser des segments, des bâtonnets et de petites sphères pour fabriquer des structures robustes, légères et complexes.
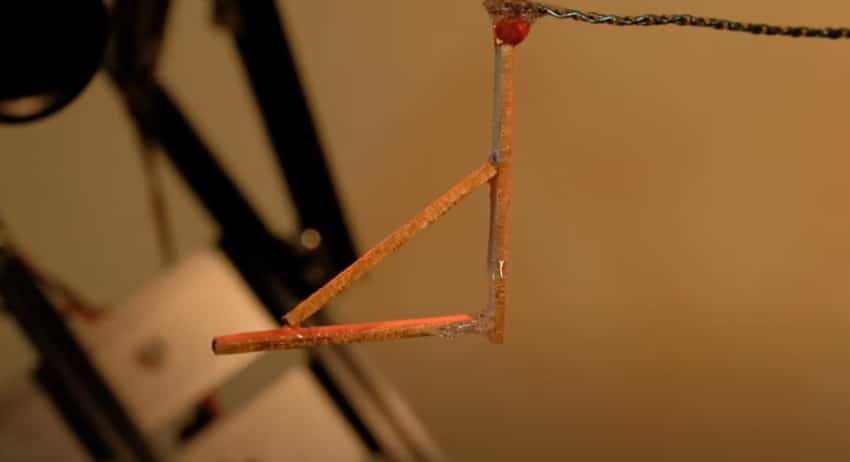
Ce système révolutionnaire sera présenté au mois d’août à Vancouver, au SIGGRAPH 2022 — l’un des événements annuels les plus importants du secteur de l’infographie et des techniques interactives. L’étendue des capacités du LeviPrint peut d’ores et déjà être visualisée dans une vidéo proposée par l’UPNA Lab.
Pour faire tenir les différentes pièces ensemble, l’équipe utilise une colle qui se solidifie sous l’effet de la lumière ultraviolette — car le système peut également faire léviter des gouttes de liquides. Il est d’ailleurs possible de fabriquer des pièces composées uniquement de colle, précisent les chercheurs, mais les structures sont généralement réalisées en assemblant des particules et des segments à l’aide de cette colle.
Pour cela, le système utilise le lévitateur acoustique pour piéger une gouttelette de colle distribuée par une seringue. La gouttelette est ensuite guidée (en lévitation) jusqu’à la position souhaitée (là où la pièce suivante sera ajoutée). Le système prélève ensuite un nouvel élément, le positionne au contact de la colle, puis utilise la lumière ultraviolette pour le séchage.
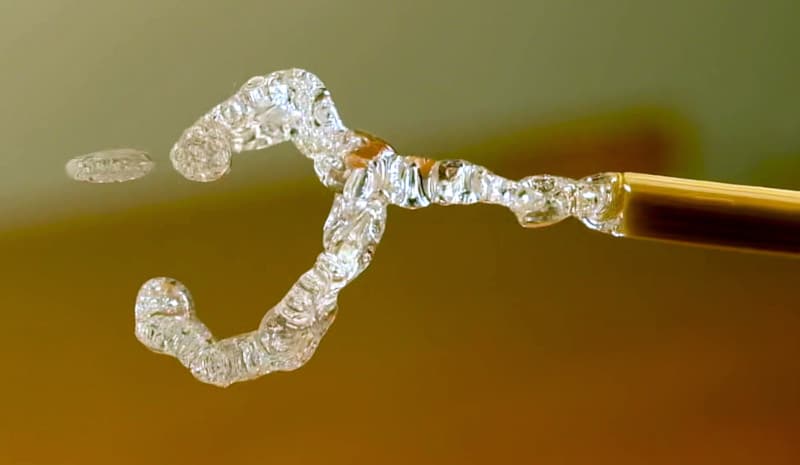
Une ouverture possible vers la fabrication additive in vivo
Les chercheurs ont analysé différents champs acoustiques en fonction de leur capacité à piéger — en position et en orientation — un objet allongé. Ils ont étudié différentes géométries de lévitateurs, équipés d’émetteurs ultrasoniques de 1 cm de diamètre. Le bâtonnet utilisé faisait 3 cm de long sur 2 mm de large et 1 mm de haut. La méthode de piégeage la plus prometteuse, appelée « Traps at Sides », consiste à générer deux nœuds de pression, de chaque côté du bâtonnet. Les prototypes fonctionnaient dans l’air à 40 kHz ; le poids maximal des bâtonnets utilisés était de 16 mg.
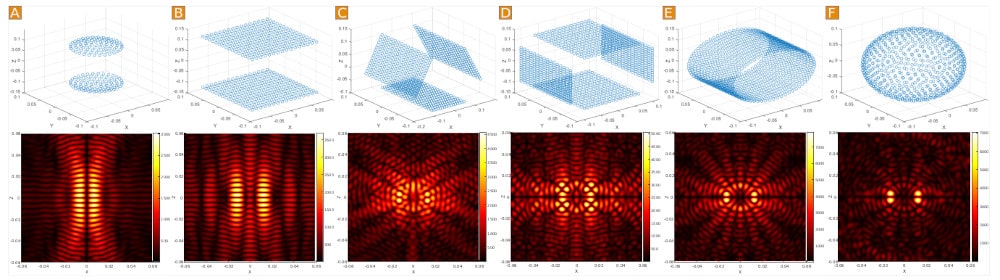
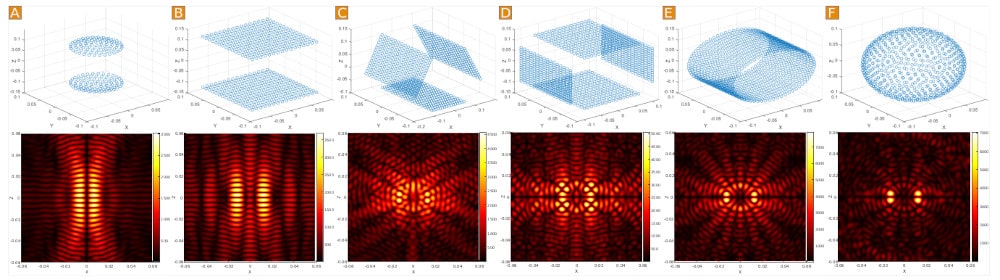
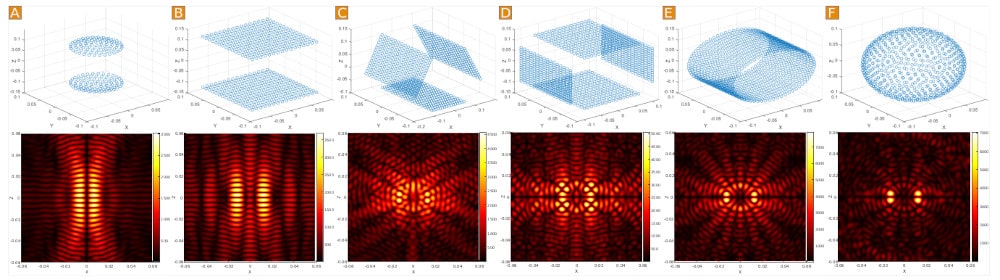
Les constructions peuvent être réalisées sous différents angles et même dans des espaces fermés. Le champ ultrasonique peut en effet traverser des tissus, des mailles et d’autres matériaux. Les chercheurs ont par exemple réussi à construire une structure complexe à l’intérieur d’un cylindre fait de mailles métalliques ; ils ont fait léviter les différentes pièces depuis l’extérieur, après les avoir insérées par une toute petite ouverture.
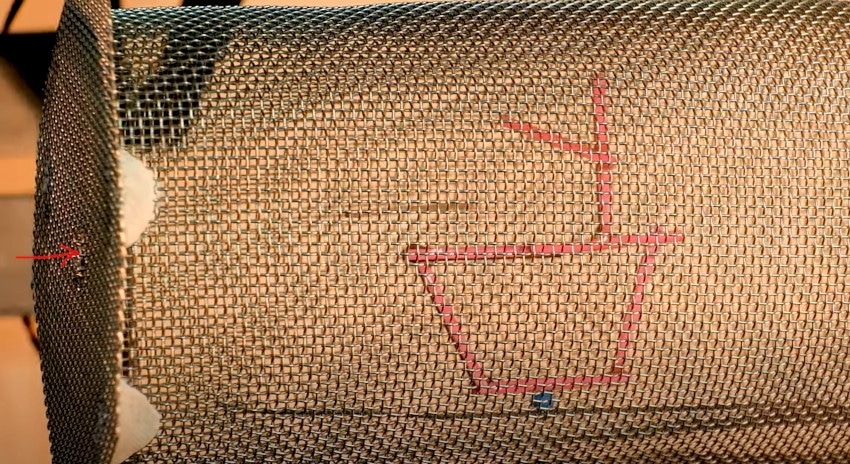
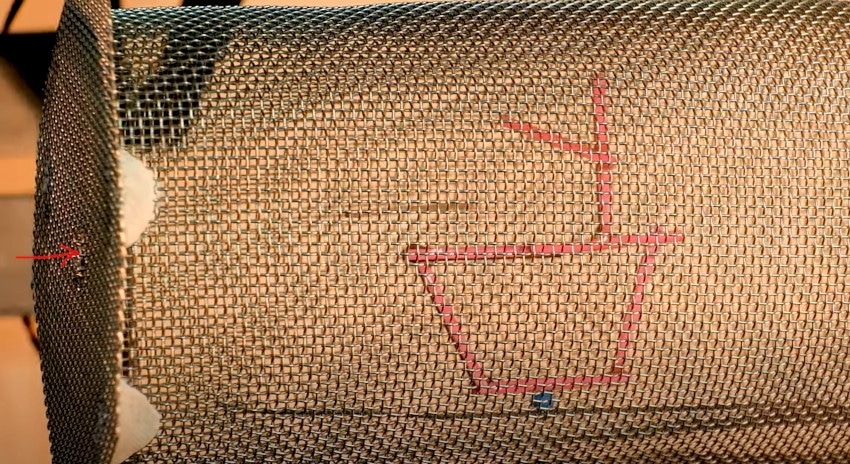
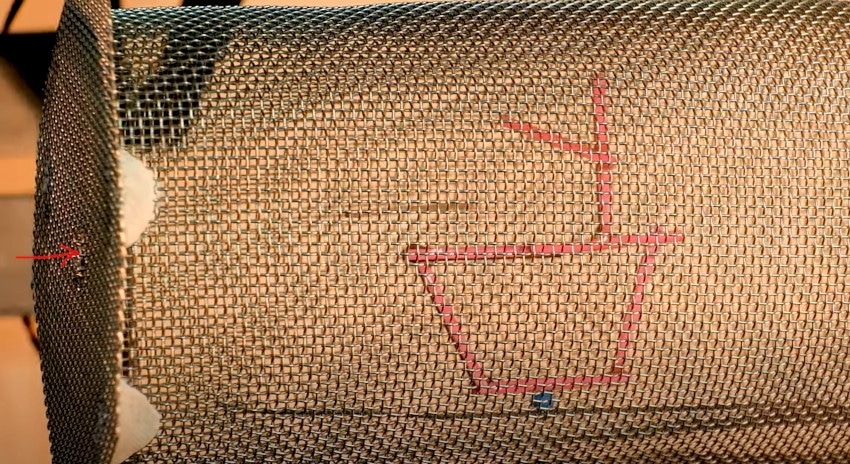
Ces possibilités ouvrent la voie à de nombreuses applications, y compris à la fabrication additive in vivo. « Si Leviprint était adapté pour fonctionner dans des milieux aqueux, il pourrait assembler des structures complexes dans des milieux de culture cellulaire et peut-être même à l’intérieur d’êtres vivants », soulignent les chercheurs. En attendant, l’équipe espère que son système inspirera de nouvelles techniques de fabrication, notamment dans des domaines tels que la microfabrication de composants électromécaniques.