L’hydrogène est de plus en plus présenté comme une solution durable à la transition énergétique. Néanmoins, aujourd’hui, 95% de l’hydrogène est produit à partir d’hydrocarbures (pétrole, gaz naturel et charbon), solution la moins coûteuse, mais la plus énergivore. De plus, trouver un matériau capable de stocker d’énormes quantités de gaz pour une application pratique reste un défi majeur. Récemment, des chercheurs australiens ont découvert une nouvelle façon de séparer, stocker et transporter d’importantes quantités de gaz en toute sécurité, sans gaspillage, sous forme de poudre, permettant une possible adoption généralisée de l’énergie à hydrogène.
Exploité depuis le 19e siècle pour alimenter les réseaux d’éclairage des villes puis pour propulser la fusée Ariane, l’hydrogène est utilisé depuis des décennies dans l’industrie où il sert notamment de matière de base pour la production d’ammoniac et de méthanol, et pour le raffinage des produits pétroliers, carburants et biocarburants.
De plus, les méthodes traditionnelles de raffinage du pétrole utilisent un processus de « distillation cryogénique » à haute énergie pour séparer le pétrole brut en différents gaz, dont l’hydrogène. Ce processus représente 15% de la consommation mondiale d’énergie, alors que la consommation mondiale d’hydrogène en représente moins de 2%.
Grâce notamment à l’avènement des piles à hydrogène, ce dernier devient un vecteur d’énergie, pouvant contribuer à décarboner certains secteurs industriels, assurer le stockage de l’énergie ainsi que la fourniture d’électricité pour des bâtiments ou le secteur des transports. Le déploiement des technologies hydrogène attend cependant de dépasser un certain nombre d’obstacles, principalement concernant le stockage et le transport, en toute sécurité et efficacement, de quantités assez conséquentes de gaz.
En effet, ce gaz est très léger, très inflammable, inodore et incolore. Il se mélange bien à l’air, les mélanges explosifs sont ainsi facilement produits. Le chauffage peut également causer la combustion ou l’explosion violente.
Récemment, des chercheurs en nanotechnologie de l’Institute for Frontier Materials (IFM) de l’Université Deakin (Australie), affirment avoir fait une percée majeure dans la séparation et le stockage des gaz. Leur découverte pourrait réduire radicalement la consommation d’énergie dans l’industrie pétrochimique, tout en rendant l’hydrogène beaucoup plus facile et plus sûr à stocker et à transporter, sous forme de poudre. Leurs résultats sont présentés dans la revue Materials Today, et leur méthode est en attente de brevets.
Révolution mécanochimique dans la production et le stockage d’hydrogène
Le professeur Chen, titulaire de la chaire de nanotechnologie de l’IFM, expose le contexte de la recherche dans un communiqué : « En ce moment, l’Australie connaît une crise du gaz sans précédent et a besoin d’une solution urgente. Une utilisation plus efficace de carburants gazeux plus propres tels que l’hydrogène est une approche alternative pour réduire les émissions de carbone et ralentir le réchauffement climatique ».
Actuellement, l’hydrogène et les autres gaz sont principalement produits par distillation cryogénique. Cette technique est réalisée sur un gaz liquéfié obtenu en comprimant et décomprimant ce dernier rapidement, provoquant son refroidissement et sa liquéfaction. En réchauffant progressivement ce gaz devenu liquide, et en jouant sur les températures d’ébullition différentes, ses différents composants sont séparés. Cette technique est cependant extrêmement énergivore.
Dans le cadre de cette étude, les chercheurs ont développé un procédé de séparation mécanochimique économe en énergie et ne créant aucun déchet. Il faut savoir que la mécanochimie est une branche de la chimie qui étudie le comportement chimique des matériaux sous l’effet d’une action mécanique, par opposition à la chaleur ou à la lumière par exemple.
« L’ingrédient spécial » du processus, comme le nomment les auteurs, est la poudre de nitrure de bore, qui est idéale pour absorber les substances. De plus, le nitrure de bore est classé comme un produit chimique de niveau 0, sans aucun danger. Concrètement, au cours du processus, la poudre de nitrure de bore est placée dans un broyeur — un cylindre — avec des billes en acier inoxydable et les gaz devant être séparés. Lorsque le cylindre est mis en rotation, à une vitesse de plus en plus élevée, la collision des billes avec la poudre et la paroi de cette chambre déclenche une réaction mécanochimique spéciale entraînant l’absorption de gaz dans la poudre.
Le Dr Mateti, second auteur, explique : « La poudre de nitrure de bore peut être réutilisée plusieurs fois pour effectuer encore et encore le même processus de séparation et de stockage des gaz ». Ainsi, ce processus peut être répété pour séparer les gaz un par un, car chaque gaz est absorbé à des intensités de broyage, pressions de gaz et périodes différentes. Dans les expériences successives, les auteurs ont réussi à séparer une combinaison de gaz d’alcyne, d’oléfine et de paraffine.
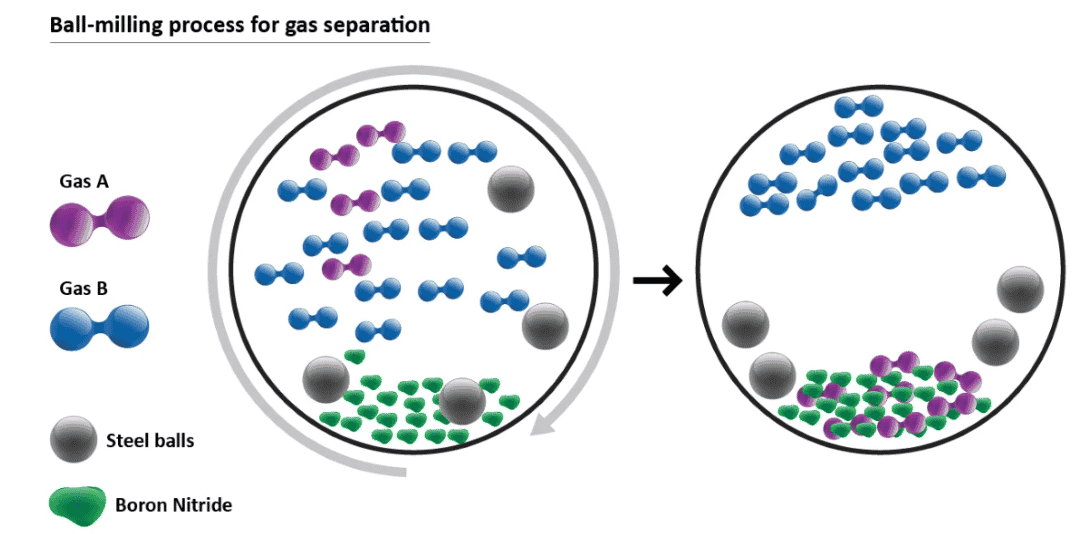
Le procédé d’absorption de gaz par broyage consomme 76,8 KJ/s pour stocker et séparer 1000 L de gaz. C’est près de 90% de moins que l’énergie utilisée dans le processus de séparation actuel de l’industrie pétrolière. Le Dr Mateti déclare : « Nous avons été tellement surpris de voir cela se produire, mais chaque fois que nous obtenions exactement le même résultat, c’était un ‘moment eurêka’ ».
Stocker du gaz à l’état solide, sans risque ni perte
Une fois absorbé dans la poudre, le gaz peut être transporté facilement et en toute sécurité, et stocké n’importe où — étant donné que le nitrure de bore est sans danger et disponible en grande quantité. Ensuite, lorsque le gaz est nécessaire, la poudre peut être simplement chauffée sous vide pour libérer le gaz tel quel. De plus, certains gaz sont libérés des poudres à des températures plus élevées que d’autres, offrant une deuxième façon de séparer les gaz s’ils sont stockés ensemble. Cette percée est l’aboutissement de trois décennies de travaux menés par le professeur Chen et son équipe. Elle pourrait aider à créer des technologies de stockage à l’état solide pour toute une gamme de gaz, dont l’hydrogène.
Le professeur Chen explique que la manière actuelle de stocker l’hydrogène se fait soit en le comprimant à 700 bar — 7 litres d’hydrogène pouvant contenir autant d’énergie que 1 litre d’essence ; soit en le liquéfiant pour le comprimer davantage à une température de -253°C — 4 litres d’hydrogène liquide équivalent à 1 litre d’essence. Les deux nécessitent de grandes quantités d’énergie, ainsi que des processus et des produits chimiques dangereux.
Il ajoute : « Nous montrons qu’il existe une alternative mécanochimique, en utilisant le broyage à billes pour stocker le gaz dans le nanomatériau à température ambiante. Il ne nécessite pas de haute pression ou de basses températures, il offrirait donc un moyen beaucoup moins cher et plus sûr de développer des innovations comme les véhicules à hydrogène ».
Enfin, l’équipe de l’IFM a testé le procédé à petite échelle, en séparant environ deux à trois litres de matière. Mais ils espèrent le soutien de l’industrie afin de mener un projet pilote complet. Sans compter qu’ils ont déposé une demande de brevet provisoire pour leur procédé.
Le professeur Chen conclut : « Nous devons valider davantage cette méthode avec l’industrie pour développer une application pratique. Pour faire passer cela du laboratoire à une plus grande échelle industrielle, nous devons vérifier que ce processus est économique, plus efficace et plus rapide que les méthodes traditionnelles de séparation et de stockage des gaz ». Ce processus mécanochimique évolutif a donc un grand potentiel en tant que méthode de séparation industrielle et peut permettre des économies d’énergie substantielles.